Historically, garages have been known more for their function than for their form and aesthetic presentation. A concrete slab, unfinished drywall, or even in some cases, bare studs. Since it’s not a living space, a garage tends to be lower on the priority list for luxuries like “paint,” “furnishings,” or “a floor that doesn’t chill your very soul to walk on barefoot.”
But while it might not be your first thought for home improvement, providing even a minor makeover to your garage floor can do wonders for how it looks—and might even enhance how well it does its job.
Do I Need a Coating for My Garage Floor?
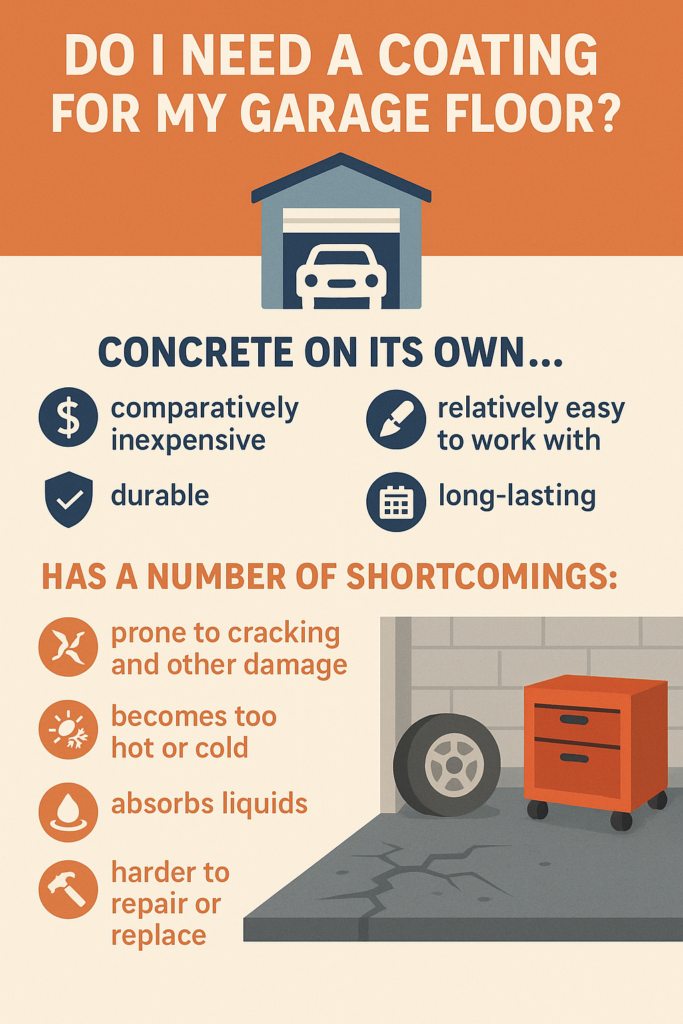
On its own, concrete has a lot of advantages. It’s comparatively inexpensive to use, and relatively easy to work with. It’s durable in ways that other materials can struggle with. And it has a surprising amount of longevity.
All of that being said, it also has a number of shortcomings, many of which people don’t think about if they’ve never worked with concrete or owned a house before:
- While durable, it’s also inflexible, making it prone to cracking, settling, and other damage.
- It doesn’t manage heat well, becoming far too hot on warm days, and far too cold on chilly ones.
- It’s porous, meaning it can absorb liquids—which can lead to issues with moisture retention, stains, and more.
- Despite its resilience, concrete isn’t indestructible, and it’s harder to repair or replace when damaged.
Most importantly, we tend to subject concrete floors to more abuse than any other flooring material, and we tend to care for it less frequently than would be prudent.
Garage floors are absolute workhorses, but that horse will start to look haggard indeed without the proper love and care. And while you can certainly treat that stone slab like your precious baby, it’s much more sensible to provide a protective covering that matches the ways the floor will be used.
What Garage Floor Coating Options Are Available?
Now that we’ve discussed the “why” a little bit, it’s time to tackle the more pressing question: “what can I cover my garage floor with?” The cop out answer here is “whatever you want.” It’s your house, after all (at least, we’re assuming; we don’t know the specifics of your situation that led you to this article). So if you can source it and install it, and aren’t breaking laws…go for it?
You’re looking for a more practical answer, though, so let’s give you one.
If you’re using the garage as an additional living space, such as an apartment, teenager’s bedroom, or the like, you can approach it the same way you would a room in the house proper. Throw down some pad and carpet, lay some ceramic tiles, install some vinyl plank, whatever matches your style, budget, and functional requirements.
Same goes for anyone repurposing the garage for indoor activities (office space, craft room, fitness studio, gaming den, etc.).
We’re going to go out on a limb, though, and assume that you’re still using the garage as a garage. In which case, you’ll want to skip the carpet and laminate flooring options. What you’re looking for is something a little more…industrial grade. Let’s break it down into a few categories.
Skin-Deep Solutions
At the bottom of this hierarchy are options that are marginal improvements at best, and extremely short-lived “upgrades” at their worst. They’ll provide a modicum of added visual appeal while they last, and may address some of the key functional issues in the immediate future, but they will wear out much faster than the rest of the concrete.
In other words, you’ll be repeating the process like you’re staining a deck, and nearly as often.
Here are some examples:
- Temporary coverings—mats, pads, rugs, and other floor “stuff” can be used to cover up the most unsightly areas, and to reduce damage from a few sources (like muddy tires or winter slush). Great if you need really cheap; terrible if you hate taking them out to hose down (among other drawbacks).
- Floor paint and floor stains—while they look nice, the moisture protection is limited to say the least, and that’s only for the brief period the treatment remains intact.
- Patches and sealers—these do a slightly better job at actually addressing problems (fixing cracks and repelling fluids, respectively), but are similarly quick to succumb to normal wear and tear.
In most cases, these approaches/products will still require prep work, and involve both cost and labor (if less on the initial application than for those mentioned below). They lose out on lifetime value, though, and if you want to upgrade your floor and have the room in the budget, it’s best to avoid these entirely.
Could-Be-Worse Coverings
In the mid-range, we have solutions that can provide fixes, minimize damage, or otherwise make a visible difference in both form and function. They’re still limited by their lack of longevity and durability, though, and will probably leave something to be desired.
Below are two examples.
Resurfacing:
This is either a dedicated product (i.e. “concrete resurfacer”), or it’s a full-fledged facelift, applying more concrete on top of the existing slab. This will, indeed, cover up cracks, chips, pitting, and other issues that develop over the life of the garage floor.
If you’ve ever seen the weathered remains of road repairs and the clear separation between the old and the new cement, though, you already know that this is merely a stop-gap: the top layer won’t fully bond to the original stone beneath, essentially leaving you with two slabs stacked atop one another.
And with the top coat usually being so much thinner than what’s underneath, it’s only a matter of time before that nice, smooth surface starts to fall apart.
Floor Tiles:
We’re not referring to ceramic or stone tiles like you might find in a bathroom. Those largely present the same advantages and disadvantages of the concrete itself.
What we’re talking about here are things like interlocking floor tiles. There are actually a few different ways this particular solution can be implemented, and distinct products for the respective approaches.
Most often, this category refers to a more robust version of the mats and pads solution mentioned above. Interlocking segments of temporary-yet-durable pads (usually made of rubber or similar materials) are installed to cover the whole floor. Individual tiles can be replaced fairly easily, and you can pick from a variety of design options to get a look you’re pleased with.
Alternatively, there are products that function as a supercharged version of some patio “tiles.” In the event you don’t actually have concrete, and you’re dealing with (or upgrading to) small grain gravel, these interlocking shapes provide frame and structure to that gravel, enhancing its stability and resilience. It’s more often implemented in outdoor settings, like gravel driveways.
Undeniable Upgrades
Finally, we have the solutions hinted at by the title of this article. These are genuinely coatings for concrete floors, and are both designed and installed with such situations in mind.
There are two primary kinds in this category: epoxy coatings, and polyaspartic coatings. Epoxy has been around for some time, and used in a variety of contexts. If you’re the handy sort (you’re reading this, aren’t you?), you’re probably familiar with its use as the bigger, beefier cousin of super glue. But it comes in a lot more varieties than that, with plenty of uses that look surprisingly beautiful.
When applied correctly, epoxy coatings seal the concrete making it waterproof. It protects the slab from spills, stains, scratches, chips, harsh salts, and an assortment of chemicals. It’s easier to repair and maintain than the concrete itself, and it feels better underfoot.
As it’s usually more affordable than polyaspartic coatings, epoxy tends to be the popular choice. If you live in an environment with stable weather patterns, predictable humidity levels, and more moderate temperature ranges, it will likely serve you almost as well as polyaspartic would.
On the other hand, if where you live is prone to drastic shifts in climate, or sees extremes in temperature (even if only in one direction), it may not hold up quite as well.
Polyaspartic coatings (also referred to as polyurea coatings) are the premium option in this category. It’s installed by professionals using dedicated tools and equipment, and the components are closer to industrial-grade, even if your installation is residential.
Of all the products and solutions we’ve mentioned, polyurea achieves the best and deepest bond with the concrete, which leads to the best longevity. It also offers better resistance to corrosion, abrasion, impacts, and the intensifying factors of temperature. It’s less likely to become brittle in the cold, and less prone to softening in the heat.
It is the most expensive option here, but it’s also the most permanent.
Factors and Parameters to Consider
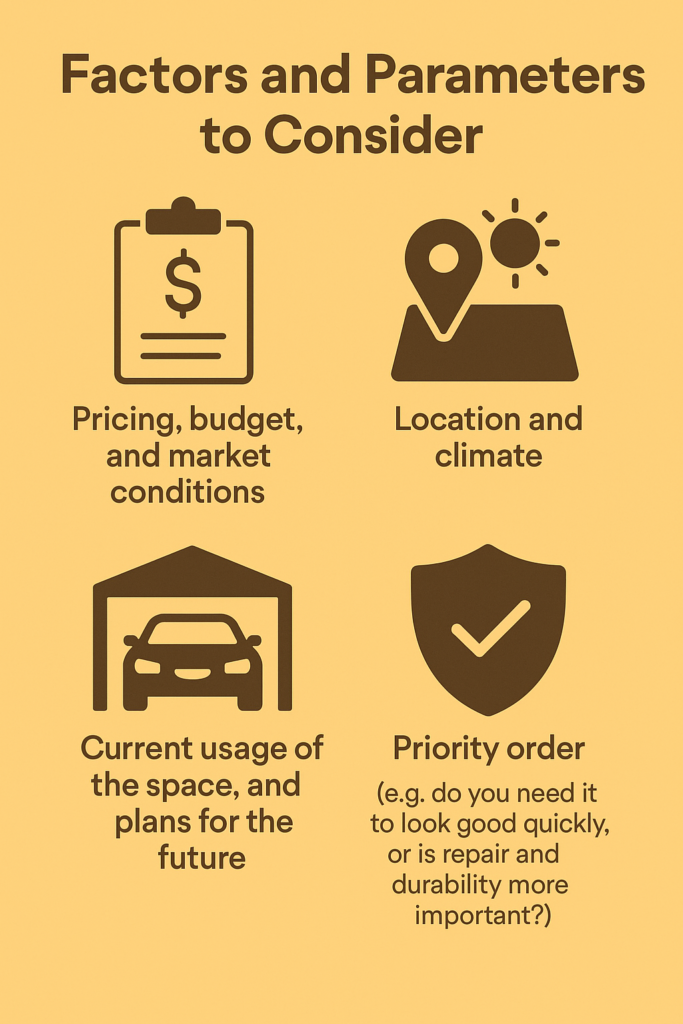
We’ve touched on a lot of this already, but while we have definite recommendations on this topic, there’s only one way a garage floor coating can be “wrong”: if it doesn’t meet your current needs (and that includes your budgetary restrictions).
In other words, we can’t tell you what to pick, because we don’t know what your parameters are. You do, though. So we suggest including some or all of the following in your considerations, as you take a look at the options available to you:
- Pricing, budget, and market conditions
- Location and climate
- Current usage of the space, and plans for the future
- Priority order (e.g. do you need it to look good quickly, or is repair and durability more important?)
How Much Is This Going to Cost Me?
Precise pricing is difficult for discussion like this. It’s not quite like picking up a new pair of shoes from a local retail location. Depending on the floor type you choose, where you live, how big your garage is, and even when you’re reading this will impact prices (and most likely leave our estimates less than accurate).
We can, however, give some admittedly broad ballpark figures based on what things look like at the time of writing.
Obviously, your least expensive options are your temporary or ad hoc coverings. In a pinch, you can cut some sections of leftover carpet rolls, and throw those down, costing you effectively nothing beyond what you’ve already spent. If you’d like something just a tad more presentable, you can opt for dedicated pads and mats, with costs mostly staying well below $200.
For those willing to spend a bit more, floor paints, stains, sealers, or resurfacing products will be the next step up. Depending on the supplies you have on hand, and how much of the labor you supply yourself, you might see a final price tag ranging from $400 to around $700 for most standard garage sizes.
With interlocking tiles, that will depend almost exclusively on the product, brand, and your square footage, with most options averaging between $2 and $5 per square foot.
Finally, for garage sizes in the 500, 600, and 700 square foot ranges, choosing high-end options like epoxy, urethane, and polyaspartic, expect to pay something between $1000 and $5000 if you’re having it installed professionally. If you opt for a simpler, DIY install with epoxy, you can edge that toward the lower end. And you’ll see proportionate changes in price as garage sizes go up or down.
Final Tips and Considerations
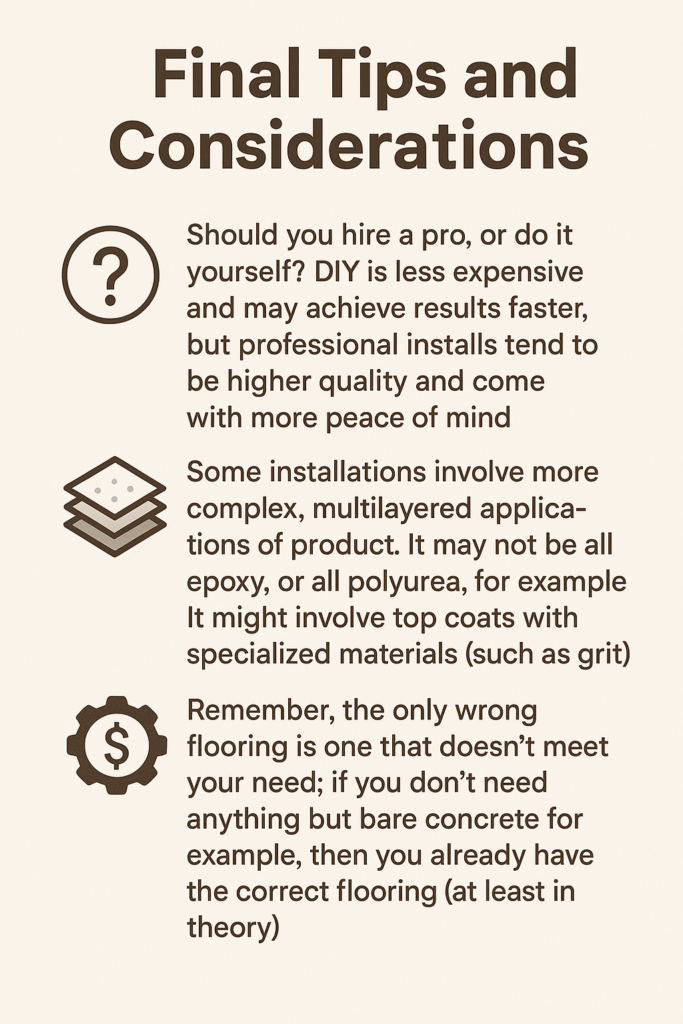
As we close out our discussion, we’d like to point out a few more decision points that may be worth mulling over. Perhaps they’ll impact your final decision, and perhaps they won’t. Only you will know for sure.
- Should you hire a pro, or do it yourself? DIY is less expensive and may achieve results faster, but professional installs tend to be higher quality and come with more peace of mind.
- Some installations involve more complex, multilayered applications of product. It may not be all epoxy, or all polyurea, for example. It might involve top coats with specialized materials (such as grit). It’s worth weighing options if you’re going DIY, and asking about available selection if you’re paying a pro.
- Remember, the only wrong flooring is one that doesn’t meet your need; if you don’t need anything but bare concrete for example, then you already have the correct flooring (at least in theory).
- Always account for ongoing maintenance and upkeep in your cost/benefit calculations. Higher end coatings cost more upfront, but tend to last longer and require less investment after the fact.
At Homeowner.org, we’re here to guide you along the way in your journey regarding all things related to buying, owning, and loving your home. Check out our site for more today.